Jet Engine Test Cell – I am the main headquarters of Delta TechOps, near the taxiway of Hartsfield Jackson Atlanta International Airport, since 1960, when the company lived in the storage area of the first aircraft – McDonnell Douglas DC-8s and Convair CV- 880s.
If that sounds tough, remember that this place has machines that weigh around 100,000 pounds. You want to make sure that the machine is not running out of time. Think of it like wearing a belt with suspenders to hold your pants up.
Jet Engine Test Cell
Source: i0.wp.com
“This investment is about expanding Delta’s business today and preparing us for long-term growth,” said Bastian. “By developing the skills of the world’s leading engineers, we will be ready to develop the technology that advances the engines and aircraft of the next generation.”
Global Customers
Back in 2015, a strong partnership between Delta and Rolls-Royce allowed the concept to grow. Under the agreement, Rolls-Royce designated Delta TechOps as an Authorized Maintenance Facility. In 2018, the relationship expanded to include branch operations.
Hanging from the top of the basket are six-foot-long, two-foot-wide instruments called coolers. They are made of special materials that absorb sound from the engine – which helps reduce noise pollution outside the building. Next-generation engines are essential to provide efficient fuel and clean power for new, larger aircraft.
Airlines will rely on these changes to help maintain profitability in the future. Delta’s new test engine was born out of a lack of new MRO tools designed for these new engines. With modern equipment it is easy to accurately measure and predict the reality of outdoor noise in the home.
In general, the chambers used are hemi-anechoic and have many features similar to Vehicle Semi-Anechoic Chambers (VSACs) used to measure noise and vibration in cars. The hemi-anechoic design means that instead of the machine being placed in an enclosed space, it can be placed on a solid surface.
Hemi-Anechoic Chambers
This is not only easy and cheap to implement but also suitable for displaying data that works in real world applications. West said he expects the next few years to bring benefits from “our investment in new engines, particularly the Rolls Royce Trent engine and the Pratt & Whitney Geared Turbofan.”
Atec Industries values our long-standing relationships with jet engine OEMs operating in the Western world. Atec has successfully completed over 30 commercial engine test projects with our leaders in the US Army and Defense Forces. Vital Link adds to test cell design, noise isolation and field service capabilities.
David Marcontell, vice president of consulting firm Oliver Wyman CAVOK, said: “The bigger the engines are delivered and on the wings, the more power is needed.” To celebrate this new facility, Delta held a grand opening ceremony with over 100 employees who were involved in the design and installation of the cell.
Source: www.rolls-royce.com
During the event, attendees heard from President Ed Bastian, US Senator David Perdue and Mitacek and Moore. The jet engine test cell will have different types of ventilation and cooling. Standard dynamometers and other test equipment are also provided.
How Big?
The design, installation and use of such rooms becomes clear when the manufacturer and contractor provide tested doors, tested and harmonized, soundproof windows, wedges, support services and technology. Atec brings 69 years of technical expertise to its engine testing program.
Our extensive testing team consists of engineers, trained specialists (SMEs), and construction and service professionals who boast decades of turbine testing and support. We employ technologists, aerodynamicists, material scientists and engineers in various fields. Our technical team uses the latest data collection and design techniques to provide the best solutions to the challenges of molecular testing.
To enter the main test room, we marvel at four 26-foot-tall concrete doors—each weighing 300,000 pounds, or 136,000 pounds. The room is 14.6 meters long and 14.6 meters wide—or 48 by 48 feet. Its bright white walls are filled with LED lights, which illuminate the concrete floor.
One wall has a large filter screen. During the test, air flows through a window from an adjacent room that brings air from outside into the building. “This new virus confirms Delta’s position as the largest and best MRO provider in North America, and will continue to allow our people to provide exceptional service and reliability to Delta and our third-party customers,
Test Cells For Impressive Range Of Turbofan Engine Families
” said Mike Moore, Vice President. – Maintenance work. “With testers and manufacturers in the same organization, we have a unique view of our customers and we continue to invest in testing technology that helps our customers produce better products,” he said.
said Hajjar. “We also recognize that our customers’ investments are very important, and they need an efficient solution to ensure that they have the most accurate and reliable data.” “Delta continues to lead the industry in innovation and safety. This exciting new technology allows Delta to build and maintain better engines and prepare them to meet the needs of a growing industry,
said Perdue. “Delta’s management and employees are among the best in the business and our continued investment will help attract the best engineers and technicians as they continue to grow. I am proud that Delta calls Georgia home.”
and I appreciate the contribution they continue to give to us. the country every day.” Delta won’t share revenue figures for test cells separately, but during a quarterly earnings call on Oct. 10, Vice President and Chief Operating Officer Gil West said that Delta’s MRO business has so far been in
Source: upload.wikimedia.org
Nothing To Show Yet
2019 is about 120 million dollars – about 23% on 2018. 150-300 units with proven machines,” said Hajjar. “So you can see that the goals and challenges are very different between a test cell and a working MRO cell.”
CEL is a leading supplier of turbofan test cells combined with strong relationships with major turbofan manufacturers and certified by multiple licenses and approvals from: General Electric, Honeywell, IAE, Pratt & Whitey, Pratt & Whitney Canada, Rolls Royce and Snecma.
CEL’s turbofan tester can weigh up to 50,000 pounds and can be used for multiple production and multi-engine applications, which greatly helps the MRO (Maintenance, Repair and Overhaul) industry to repair and upgrade different types of jet engines.
. “Delta Cell is focused on quality,” said Joe Hajjar, MDS vice president of business development. “They’re in and out of the test center quickly to get their engines back, but the new Rolls-Royce center will focus on research and development, where test engineers push the engine to its limits by gathering lots of data.
Growth Drivers
as possible.” If jet engines cause noise on the runway, consider testing them in factories and test facilities. The jet engine test cell (ENTC) should not be subject to noise and other health and safety issues: Sound should also be properly controlled to provide efficient performance and vibration information. Nearly 60 years later, Delta TechOps maintains its own fleet of over 900 aircraft with aircraft for customers over
150, including Hawaiian Airlines, Virgin Australia and UPS, as well as military and government aircraft. It has dedicated its new test cell and engine storage to more than 7,000 engines over the next 30 years. As part of the company’s investment
$150 million, or about $194 million, in the UK aerospace industry – Hajjar said the Rolls-Royce virus probe will be used with state-of-the-art technology, including an internal combustion engine scanner. by taking X-ray image. will be Ray.
The walls of the room will be 5.5 meters or 1.7 meters. A tec, Inc. is the supplier of choice for the TurboFan testing, construction, maintenance, and repair industries. Our highly skilled engineers and extensive network of equipment and resources provide our customers with unparalleled expertise and value for complex and demanding testing projects.
Design Challenges
“At MDS, we believe we are changing the game by enabling OEMs to test, quickly and easily,” said Hajjar. “We are talking about the new IT technology we have developed to measure a million tons per second with zero loss, with absolute certainty.”
Source: d1ldvf68ux039x.cloudfront.net
Don Mitacek, Vice President – TechOps said “This new test cell is not only good for the future of Delta, but also for our engineers and future engineers.” “The efficiency and experience of our people is the reason why we can invest so much in the future. They really leave a legacy with a new test cell and machine – this whole place shows their achievements. .and the commitment of our people.
Typically, when an engine comes through Delta TechOps, technicians will disassemble, inspect, repair and reassemble it. Finally, it goes into the lab for testing. If it doesn’t pass the test lab, the engine is sent back to Delta’s engine shop.
to continue viewing. The test cell, which is the first cell produced by a US airline in more than 20 years, is capable of running the engines at full power and 150,000 pounds of thrust. By comparison, the cell
The test plane has a torque of over 68,000 pounds and the most powerful engine in the world today, the GE90 that powers Delta’s Boeing 777-200LR, is rated at 115,000 pounds. world at Delta TechOps at Atlas
nta, it is clear that you have entered a room designed to support the next generation of turbofans. Opened for business last February, the $100 million building has large, complex and complex machines running through it.
This is where you can save your favorite articles so you can return to them easily. Sign in or sign in to your account to save your favorite articles or read them later. A new engine testing facility in Atlanta, Georgia—Delta TechOps—opened earlier this year.
It is, at the moment, the largest experimental cell in the world. It is designed to fit the engines currently in use, as well as future engines that have not yet been built or are in operation.
CEL works with you in a team approach, combined with collaboration with engineering manufacturers, local contractors and subcontractors, to create the most efficient, cost-effective and efficient solution for your needs. CEL can also provide you with a cell designed for your business, allowing a quick turnaround to test different types of engines in one place: turbofan, APU, helicopter and turboprop engine.
Today, Delta TechOps leaders and employees cut the ribbon, opening the largest jet engine test cell in the world. And although the world’s largest is a good thing to be proud of, there is a lot of research, creativity and thought that went into creating this world-class tool.
In October 2015, Delta and Rolls-Royce signed an agreement for Delta TechOps to become an Authorized Maintenance Center for Rolls-Royce engines. Under the agreement, the airline will provide engine support for the new Rolls-Royce Trent XWB, Trent 1000, Trent 7000 and BR715 engines.
jet engine test cell design, engine test cell equipment, aircraft engine test cell, aircraft engine test cell facility, jet engine test cell operator, jet engine test cell manufacturers, aero engine test, engine test cell design
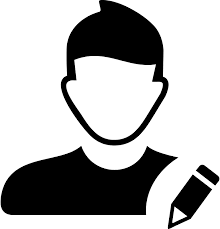
Welcome to my website! Here’s a brief introduction about me.
I am Charles Pham, a passionate individual with a diverse range of interests and experiences. Throughout my life, I have pursued my curiosity and embraced various opportunities that have shaped me into the person I am today.